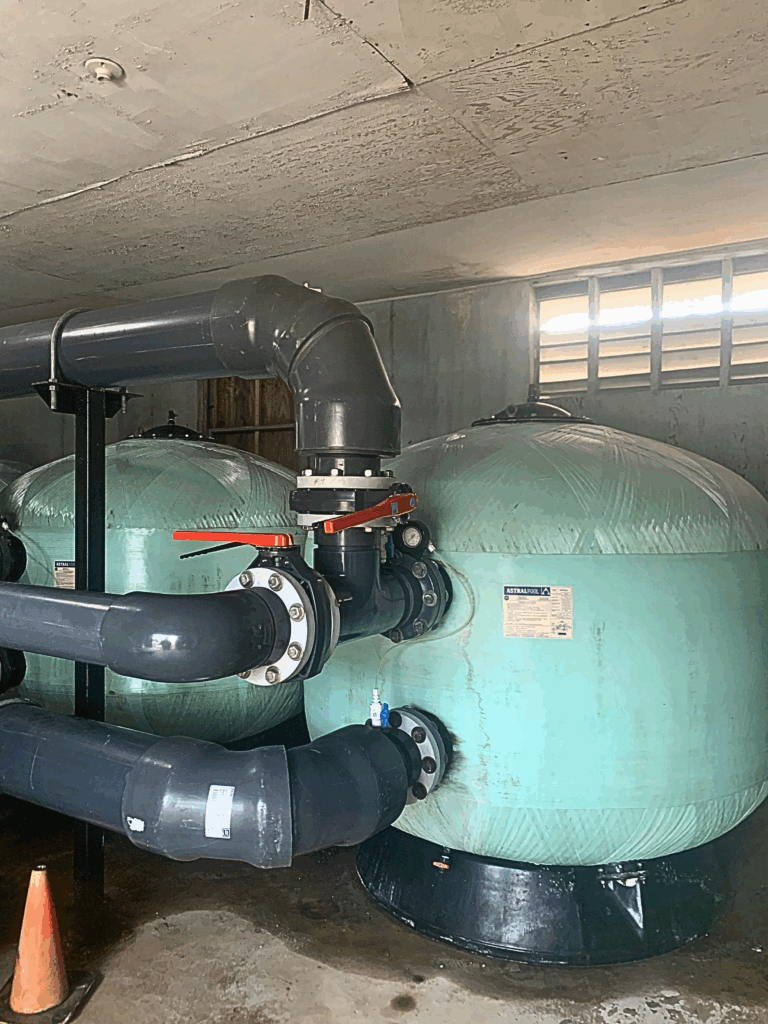
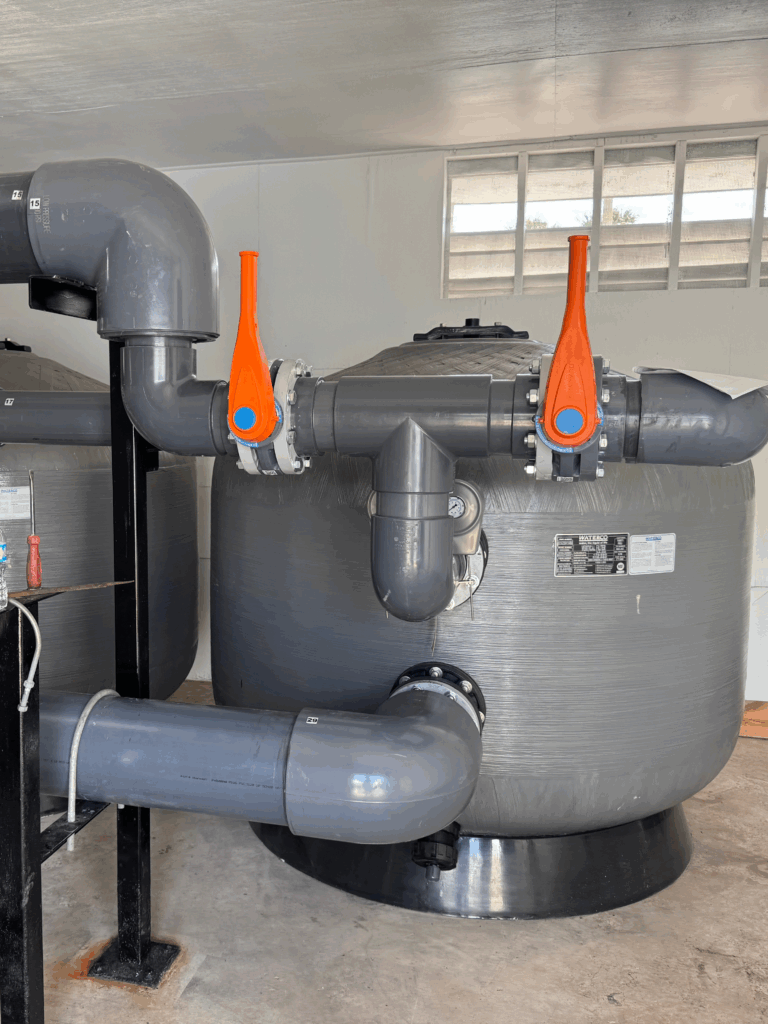
Problem
The community pool at Naval Air Station Jacksonville was facing significant issues with its filtration system. The existing filters were cracking and deteriorating, putting the facility at risk of operational shutdown. A local pool contractor on the job needed a rigging partner with the equipment and manpower to remove the old filters and assist in assembling and re-piping the new system.
Coker was initially brought in to provide supplemental labor support. However, as the project progressed, it became clear that additional resources and coordination would be necessary to complete the work within the tight timeline.
Strategy
Our team began with a small crew and quickly adapted to meet the project’s demands, remobilizing and doubling manpower to complete the filter assembly within a week. The job required careful navigation of the jobsite’s limited access and indoor space constraints.
We used a Lull (off-road forklift) and qualified riggers to maneuver the large filters into the building and position them correctly. While the job didn’t require any specialized certifications, it called for a skilled team that could safely handle heavy equipment and work precisely in confined spaces. Our team took extra care to ensure the finished assembly looked as good as it performed.
Outcome
The project was completed successfully, on time and under budget. The client was extremely pleased with both the quality of work and the professionalism of our crew. In fact, our performance on the job led to a new connection with another contractor on-site, who has since reached out for support on additional projects.
This job met all functional goals and exceeded expectations in terms of fit and finish. It was a strong example of Coker’s ability to adapt quickly, deliver high-quality results, and build long-term partnerships through reliable performance.